My Experience and Projects
Showcasing my experience throughout my mechanical engineering career.
Autonomous Vehicle Mobility Institute
The Autonomous Vehicle Mobility Institute (AVMI) advances research in modeling, control, and testing of autonomous and manned vehicles for harsh terrain and adversarial environments. Supporting the U.S. Army GVSC, AVMI collaborates with government, NATO, academia, and industry, and extends its work to systems like rovers, tractors, and off-road machinery.
Currently, I’m part of a team building a high-fidelity driving simulator to replicate the experience of operating the lab’s off-road autonomous ground robot. This simulator aims to provide an extremely immersive experience, incorporating real-time terrain interaction, vehicle dynamics, and operator controls to mirror real-world driving conditions. It's being developed using game engine software integrated with robotics middleware to create a seamless simulation environment. The project serves multiple purposes: it offers a safe and cost-effective platform for testing autonomous algorithms, supports human-in-the-loop experimentation, and provides a training environment for future operators. This effort requires collaboration across disciplines, including mechanical design, software integration, and control systems, and has allowed me to further develop my skills in systems engineering and user-focused design.
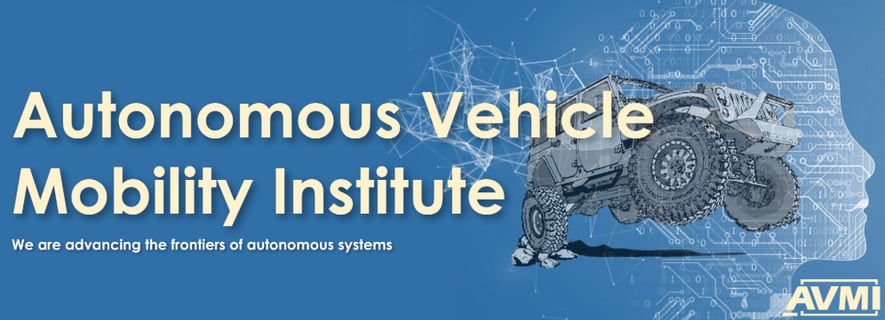
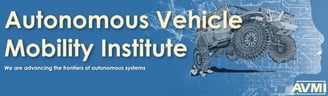
During my time at the lab, I contributed to both mechanical design improvements and ongoing research efforts focused on vehicle autonomy. One of my key tasks involved addressing a persistent issue in the gear reduction system—the gasket in use was prone to wear and failure under heavy loads and extended testing conditions. After researching alternative materials and analyzing the system’s mechanical constraints, I designed a new gasket using a more resilient and heat-resistant material that could better withstand the stresses of off-road vehicle operation. This change not only improved sealing and durability but also reduced the frequency of system maintenance and failures during testing.
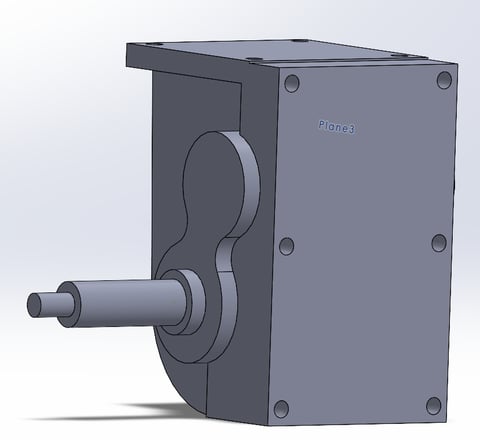
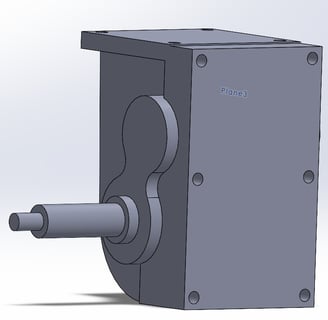
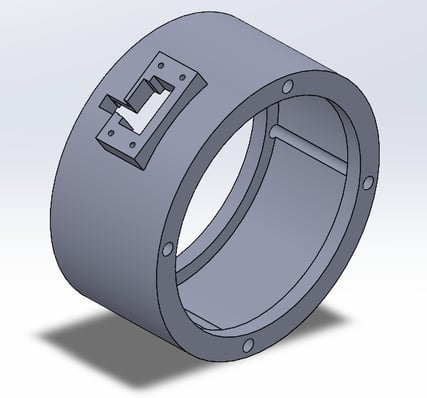
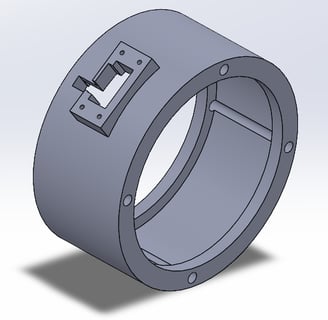
Another challenge I worked on was the wheel speed sensor, which was giving inconsistent readings due to misalignment and vibration. I conducted a detailed review of the mounting setup and ultimately redesigned both the housing and the attachment bracket. The new design stabilized the sensor, improved alignment, and incorporated vibration-dampening features to ensure more accurate and consistent speed data—an essential input for the robot's navigation and control systems.
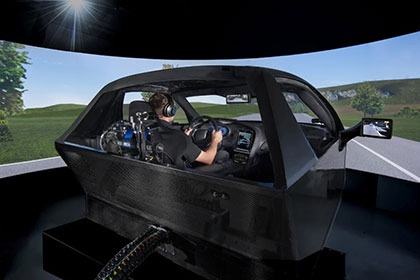
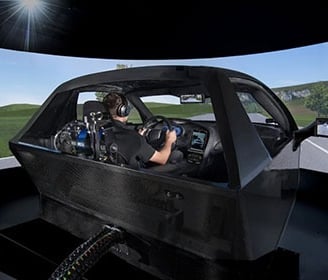
Medical and Manufacturing Innovation (MedMain) Laboratory
MedMain advances engineering science and technology to improve healthcare by applying robotics, manufacturing, and design for safer, more efficient, and cost-effective medical solutions. Bridging science and clinical application, MedMain produces research, patents, and innovators. Projects include robotic artery grinding for cardiovascular treatment, stroke therapy via high-speed clot machining, tele-ultrasound systems, robotic neuro-intervention, mechanical testing of biological tissues, and polishing 3D-printed internal channels.
As part of a project focused on post-processing techniques for metal additive manufacturing, I worked on developing innovative solutions to improve the surface finish within complex internal channels, which are often inaccessible using conventional polishing methods. These channels, commonly found in aerospace and heat-exchanger components, tend to have rough internal surfaces due to the nature of metal 3D printing, which can negatively affect fluid flow, pressure loss, and overall system performance.


My primary contribution was the design and enhancement of a specialized polishing mechanism capable of reaching and refining these internal surfaces. The device had to be compact, precise, and adaptable to a range of channel geometries. I experimented with different tool head materials, abrasive mediums, and actuation methods to improve effectiveness while ensuring the mechanism could navigate bends and variable diameters within the channels. Through iterative prototyping and testing, I optimized the tool for maximum reach and consistent polishing results, significantly improving internal surface quality without damaging the part's structure.
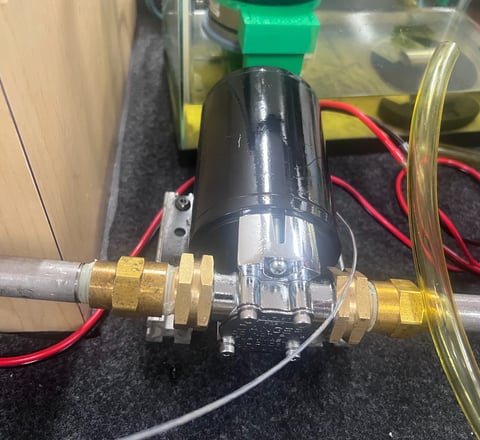
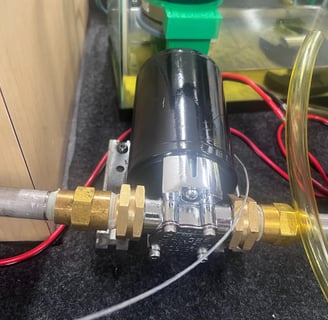
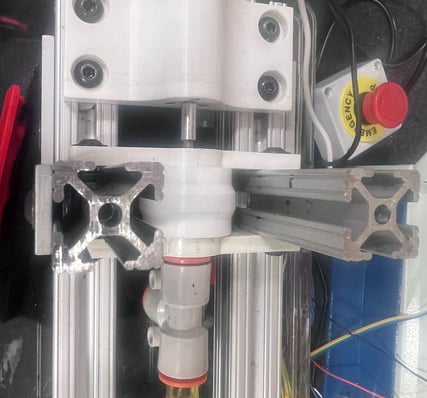
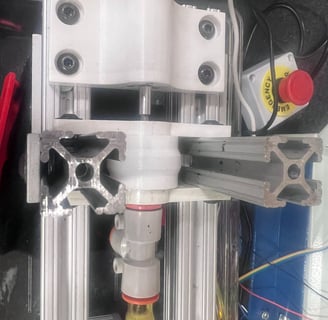
In addition, I helped develop a micro-sanding device designed to operate in ultra-narrow channels—some as small as a toothpick in diameter. This required precise engineering to balance mechanical flexibility and strength, while ensuring the device did not obstruct or deform the channels. I also contributed to optimizing the fluid dynamics within these channels, adjusting polishing parameters to enhance flow efficiency and reduce turbulence post-processing. This work was crucial for advancing the viability of metal additive parts in high-performance fluid systems, where internal surface quality is critical to function.
About
Showcasing my journey in mechanical engineering.
Contact ME
marcgk25@gmail.com
+1(347)-265-6614
© 2025. All rights reserved.